Projectname: AGANFOILS – As Good as New Foils. Projectnumber: LIFE15ENV/NL/000429.
Challenge against Business Case and the future
During the project we experienced challenges in relation to the Business Case. We also look at the future of the LIFE AGANFOILS project.
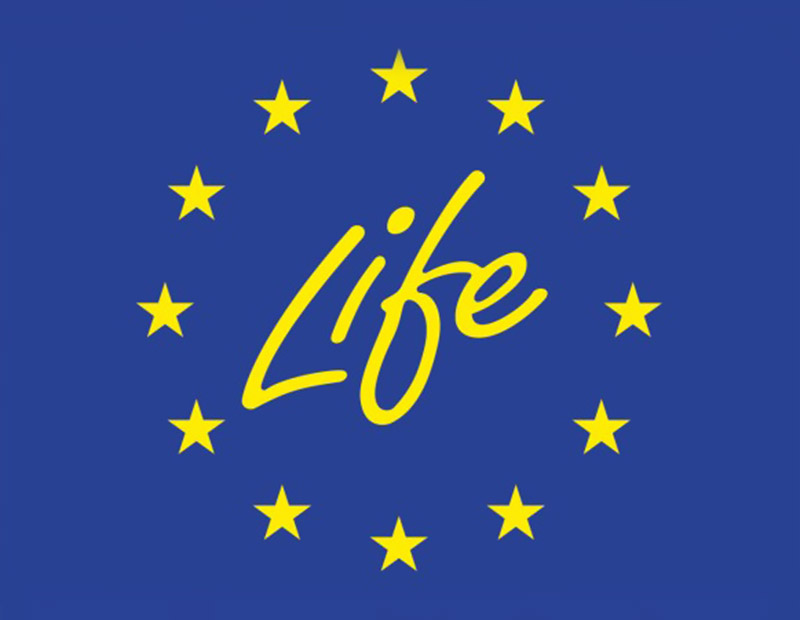
Challenge
The project has now reached the point that it has produced a stable recycling process to recycle LDPE-foil to a reusable LDPE-regranulate, that is suitable for use to produce new foil.
The market conditions are very uncertain at the moment, caused by the economic developments, COVID-19 and limited demand for regranulate.
Mandatory reuse of regranulate in new plastic-applications will increase the demand for this product. The price-differences between virgin plastics and our regranulate are momentarily, also caused by the relatively low oil-prices, too small and producers don’t have a lot of incentive to use regranulate.
Attero is waiting for clarity concerning regulation. These developments will take place in the near future, both at national and at European level. As soon as this becomes clear, this will offer Attero the frame to duplicate this project well and to get advancement with interested parties.
A number of issues that threaten our project, are incineration and CO2 taxes on waste-to-energy of these residue streams. This is imposed on our industry, where other industries don’t have to deal with this. A level playing field for our regranulate and an mandatory reuse in new plastic-applications will be needed in order to be able to compete with virgin plastics long term.
Also Attero had decided to produce the regranulate for 100% of foil that is won out of municipal waste. As a consequence of the high degree of contamination of the waste, the recycling process is all the more challenging and complex. Also Attero applies high standards in regard to the environment, work safety and the application of recycled materials. Customers of Attero process the regranulate only in applications where the use of virgin plastics is displaced.
This in contrast to the recycling processes that is applied in surrounding countries:
- The regranulate there is mostly produced from recycled industrial waste (mostly clean) with a usually constant composition (for instance obtained from the packaging industry).
- Also elsewhere in Europe, under the title of certified recycling, sorted out plastic is being used as fill-in material in for instance the concrete industry.
The government should for instance have to buy new products that contains a minimum recycled content, which has been anchored in recycling-goals. This is now limited to 10%. If everyone would buy only 10% of the products that have been produced in a circular manner, than we would linger on a recycled content of 40%.
The business case of the project has not been as good as expected because of the market situation (low oil prices, low virgin prices and a relatively low demand for recycled content due to these prices and COVID). The European Commission is addressing these market dynamics effectively. Attero is seeing the first signals in the market that the anticipated mandatory application of recycled content will have a positive impact. Some European countries are already implementing incentives for producers to apply recycled content via EPR schemes and taxation. The swift implementation and reinforcement by the European Commission of this proposed legislation will certainly support a positive price trend to make the project economically interesting. The current recovery of the oil prices is also helping us to see an improvement in the market conditions.
The future
Finally we need a good overview on where the plastics market is going. Some producers want more kinds of plastics, while sorting companies and plastics recyclers want less kinds of plastics. Especially the development of biodegradable plastics is considered a major threat by Attero. E.g. in case plastic film is replaced by biodegradable PLA film.
We also see new kinds of plastics coming onto the market to replace virgin plastic film. Bioplastics that have the same characteristics as virgin plastics can be recycled easily in the current recycling infrastructure. For example, bioPE is a PE plastic that is made from a biobased feedstock, but can be recycled into new PE just as easily as virgin oil-based PE. This makes bioPE score very well in a life cycle analysis (CO2-score) compared to virgin oil-based plastics. It is quite different however for biodegradable PLA film plastic. Consumers have difficulty distinguishing PLA film from other kinds of film, so are likely to dispose PLA plastic with their other plastic packaging waste. When the feedstock for the Attero film recycling plant contains only a few percent of PLA film in the LDPE film the quality of the LDPE regranulate will deteriorate and make it impossible to blow film from the regranulate again. There are currently no recyclers who can turn biodegradable PLA into new PLA again. And many countries forbid biodegradable PLA to be disposed off with the biowaste because it deteriorates the compost quality and provides no environmental benefits (e.g. Germany, Belgium, Netherlands).