Projectname: AGANFOILS – As Good as New Foils. Projectnumber: LIFE15ENV/NL/000429.
Context van het LIFE AGANFOILS project
The initial focus of the AGANFOILS project was on sustainable and efficient upcycling of LDPE plastic waste foil from MSW-streams (Municipal Solid Waste) at the location of Attero in Wijster, the Netherlands. In this waste-to-resource solution, Attero contributes to diminishing the impact of plastics on the environment. By investing in the plastics reuse chain, Attero provides a high quality reuse of 25,000,000 kilos foil from domestic waste collection. To understand the environmental problem targeted with the AGANFOILS project, below a description is provided of the environmental impact of the disposal and current recycling method of plastic waste foil.
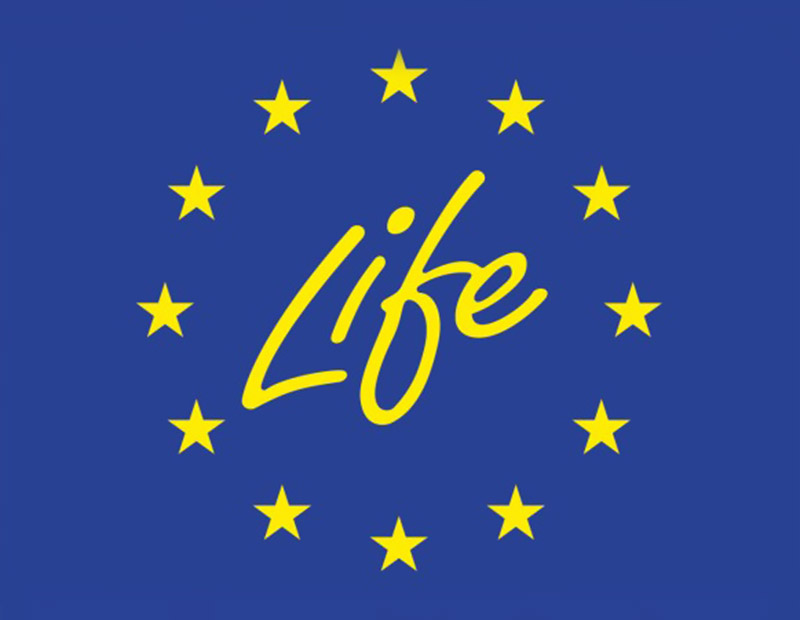
At present day, in Europe a small but steadily increasing share (26%) of plastic waste is being recycled. With regard to plastic waste foils recovered from MSW (Municipal Solid Waste), the level of contamination has a negative influence on the environmental impact of the recycling process, being:
- Only a part of the plastic waste foil that is recovered from the treatment and sorting process, is due to quality restrains of suitability for recycling. Pre-treatment of the foils is necessary.
- Due to the relatively high level of contamination a resource-intensive treatment of the foil is required. Our recycling-process contains several ways of grinding, washing, water-based separators (Sink-float), mechanical cleaners, thermic heaters and dryers. The amount of energy and water that is needed for the recycle-process is considerable. For this, Attero uses sustainable electricity and steam, which is provided from Atteros Waste to Energy unit. Compared to the energy consumption at the production of virgin plastics, the energy consumption in our recycle-process is far more energy efficient. Furthermore, as there is only a small number of recyclers available in Europe (f.i. Germany), a lot of transport is needed between the waste-processing companies and waste-sorting companies on the one side, and the waste-recyclers on the other side. The yearly distance used for transport of the sorted foils, which is carried out by Attero, is 4,800,000 km. This means a CO2-emission of 550 tons/year. By building the PRP, this transport will be avoided and the mentioned CO2-emission is prevented.
The current recycle-processes are not able to sufficiently reduce the contamination level, negatively effecting the quality of the recycled regranulate. To meet the quality requirements for high end applications (for instance blown film) an extensive cold and hot washing process, such as that from the PRP is a necessity. Currently the AGANFOILS process is operational. Attero invested in an innovative and one of a kind process for the reuse of LDPE plastic waste foil from the domestic waste collection. Our Polymer Recycling Plant (PRP) is integrated in Attero’s current collection, pre-separation and sorting facility in Wijster the Netherlands. By using state of the art equipment in a smart sequence and combining the recycling stage with the already existing process, an integrated waste-to-resource waste management process has been realised.
By introducing an innovative hot washing step in the plastic foil recycling process we are nowadays capable of producing a high-end regranulated quality that can be used in high end applications like blown film foils. The integration on one geographical location enables the elimination of the transport to an external recycle facility, basically eliminating the transport distances significantly. The circular plastics economy can be witnessed in Wijster.
Valuechain
Attero’s PRP is now considered a best practice* within Europe, also by CEFLEX. CEFLEX is a collaborative European-wide initiative representing the entire value chain of flexible packaging, including 180 producer responsibility schemes, packaging producers, sorting and recycling companies, etc. Attero organized tours for a CEFLEX delegation, joined Group meetings and discussions to share our insights. European packaging producers now realize that the European plastic packaging recycling targets can only be achieved when also Attero’s infrastructure for post-separation and sorting in combination with a PRP-like recycling installation is being duplicated. CEFLEX recently published a position paper on preferred collection systems for flexible packaging (plastic foil) in which this is confirmed:
“Separate collection of flexible packaging at source is preferred. Flexible packaging can be combined with other packaging, including rigid plastics, metal and beverage cartons. Since a relevant proportion of flexible packaging may remain in the mixed solid waste stream, the additional sorting of flexible packaging from the mixed waste is necessary to maximize recovery and enable circularity. With the appropriate infrastructure, existing practice shows that these materials can deliver comparable quality recyclate. If separate collection is not viable, mixed waste collection and sorting flexible packaging from mixed waste is an alternative collection option” (source: www.ceflex.eu/resources).
Future
Attero also sees opportunities towards the future. For the near future we expect to even expand our recycling capacity for plastics at the PRP and within the circular plastics chain of Attero as a whole.
The yield of the PRP will improve by making use of the non-LDPE plastics and will transform the content in such a way that our (from the PRP) residue plastics will be reused in processes and applications that allow a mix of plastics and contamination levels that are included. As soon as reuse of plastics in non-food applications will become mandatory Attero considers additional investments in either a 2nd PRP recycle facility, or by upgrading some of our plastic feedstock products as produced by our Plastic Sorting facility. The current economics force Attero to focus on the thick-layered market-applications for our regranulates at this moment. However we have proven to be capable of producing blown film quality regranulates at our PRP production facility. As soon as the economics allow (price / supply and demand) we will shift our sales to these high end applications.
* Are you working on a LIFE-project and interested in best practice? Please contact Aleksejs Zitkevics.